What is Ore Sorting?
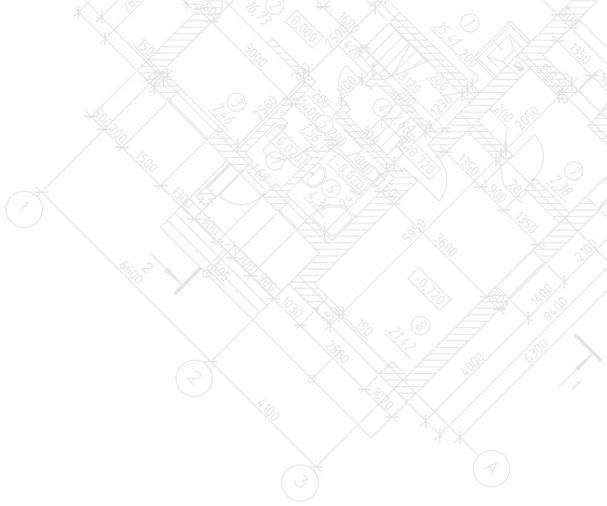
HPY SORTING
What is ore sorting?
Ore sorting is a physical sorting method that uses external forces to separate ore from waste rock by testing and identifying each ore individually based on its physical characteristics. These characteristics, such as color, luster, density, reflection, and refraction, are detected by optical or electrical sensors and analyzed to sort the ore. By using ore sorting technology, it is possible to efficiently separate valuable minerals from the waste rock, leading to cost savings and improved mining operations.
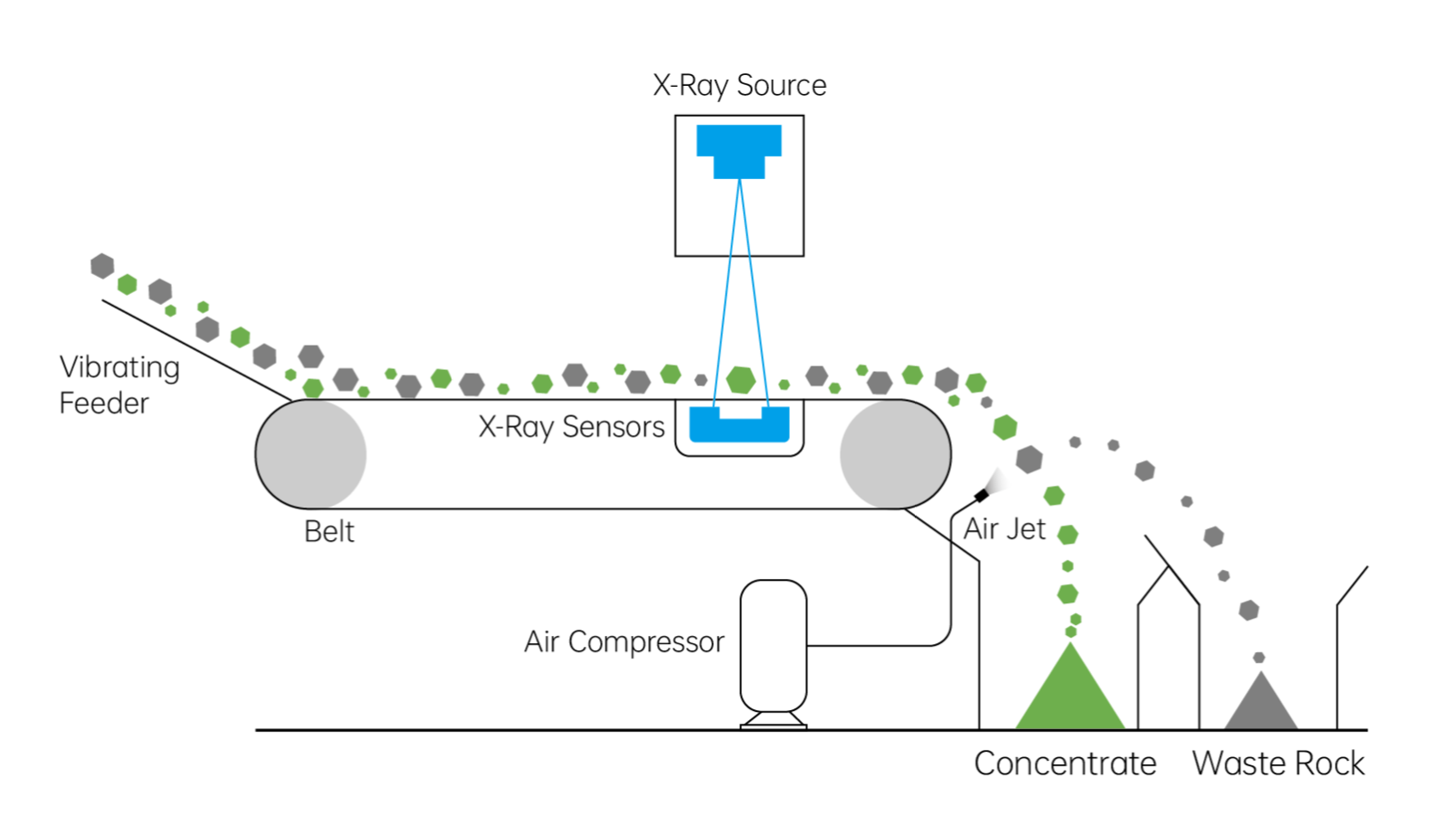
Sensor-based ore sorting has been used in the mining industry since the 1970s, but recent advances in artificial intelligence, deep learning, machine vision, and image recognition have greatly improved its effectiveness. XRT X-ray sorting technology with deep learning functions, in particular, has the potential to comprehensively utilize low-grade ore resources. This technology can enrich low-grade ore, waste rock, and deemed valueless stockpile waste rock into concentrate with industrial mining value and comprehensive utilization potential. These cutting-edge technologies have opened up new possibilities for the efficient and sustainable utilization of resources.
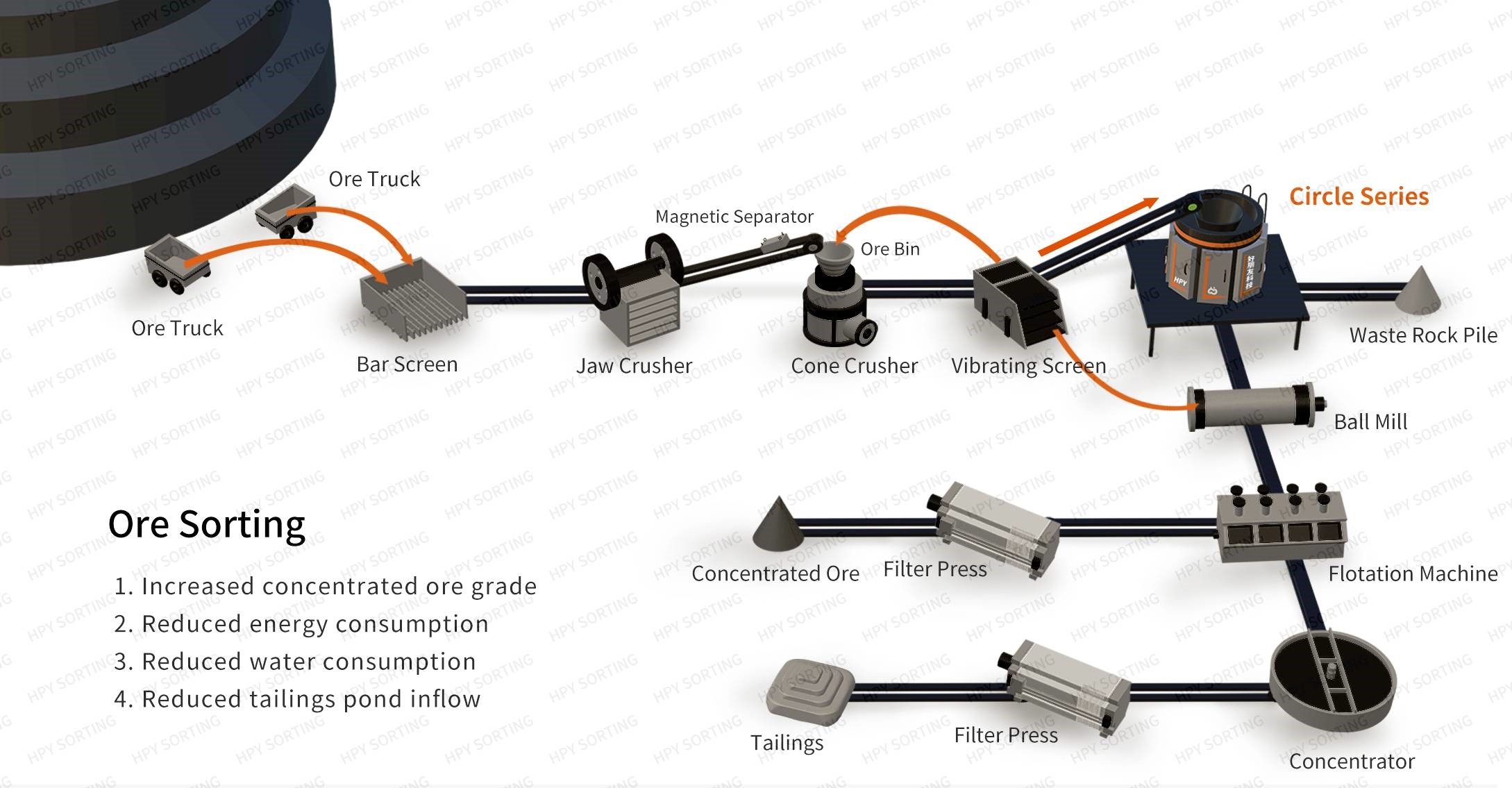
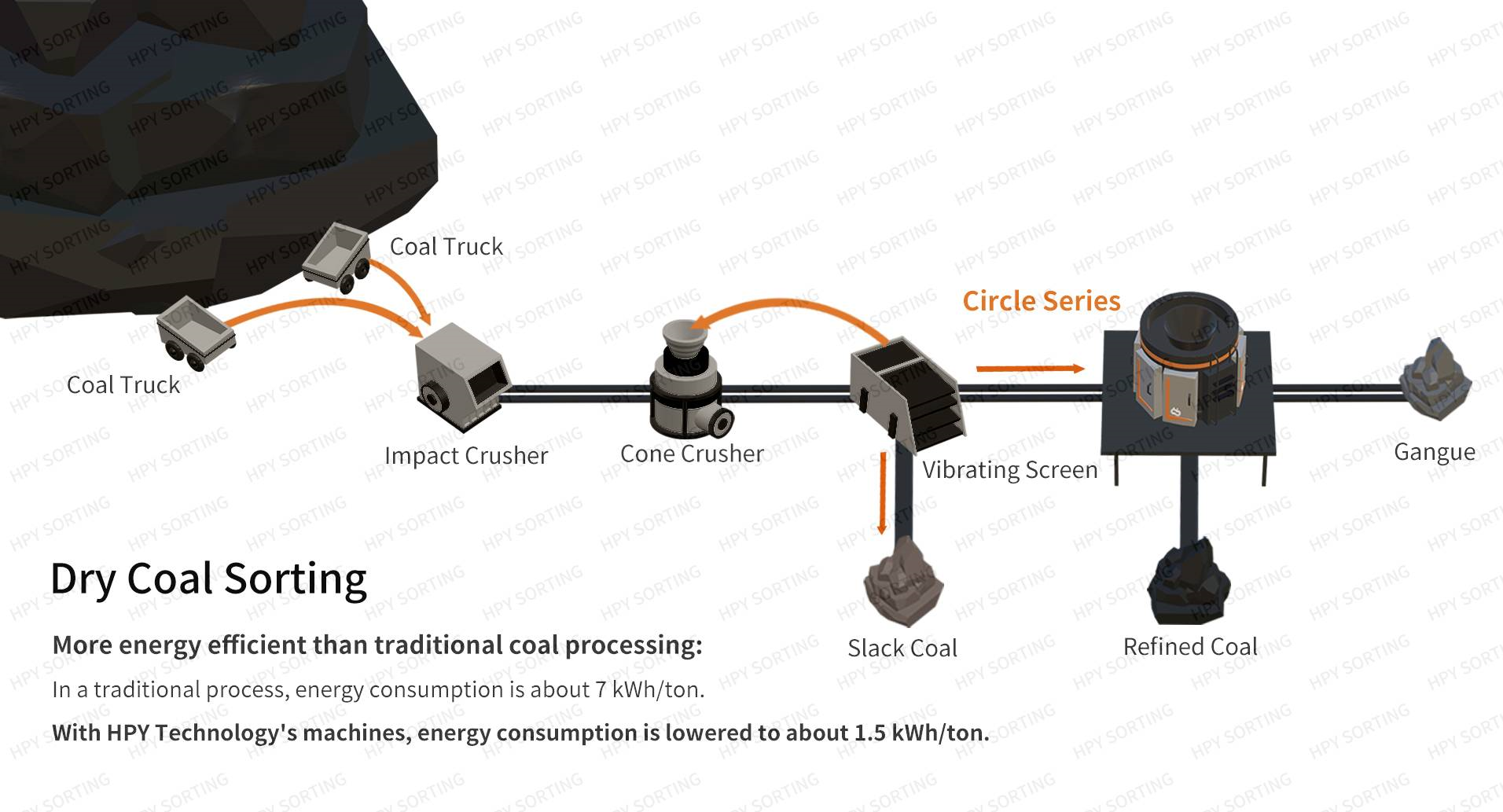
HPY Technology utilizes both a combined detection method that incorporates a VIS HD dual-sided imaging system and X-ray technology, which can be customized based on the specific characteristics of different ores. HPY has also developed an AI algorithm specifically for ore sorting, called the Wenshu Algorithm. This algorithm applies deep learning theory to the mining industry, allowing for the development of an adaptive ore sorting model that can track and optimize itself in real-time based on changes in ore grade. In complex ore sorting environments, the ore sorting model can adapt its structure to accommodate different characteristics such as ore size, texture, luster, and thickness in order to achieve accurate identification.
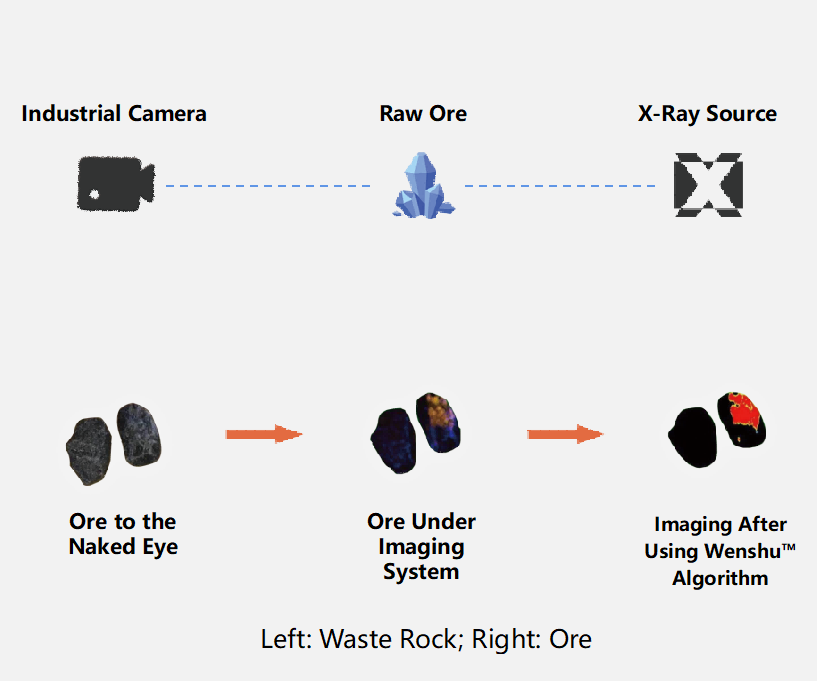
News & Media
ORE SORTING’S APPLICATIONS
Since its inception, HPY Technology Co., Ltd. has chased the goal of innovating and transforming ore sorting. As a part of the “new mining revolution”, HPY has dedicated itself to ensuring the best products for its customers, that deliver great results with excellent service.
Mineral Processing Plant Sorting
The most common application for sensor-based ore sorting machine is actually applied at the Mineral Processing Plant! HPY’s XRT and VIS-HD colour sorting technologies can reduce labour demand, increase the feed grade of the ores going into the plant, thereby maximizing each hour of grinding and minimizing the tailings pond.
Waste Rock or Low-grade Ore Sorting
One great asset yet to be explored and utilized by mining companies is the Waste Rock Pile or Low-grade Stockpile currently occupying countless acres of land and causing potential environmental hazards! HPY’s XRT and VIS-HD colour sorting technologies help mines expand their resource estimation and create potential additional revenue from the processed construction aggregate.
Underground Ore Sorting
🔹Upgrade Run-of-Mine (ROM) Grade On-Site – Pre-concentrate ore underground to boost head grade before it even reaches the surface.
🔹 Expand Reserves – Tap into low-grade zones that would otherwise be uneconomical.
🔹 Cut Hoisting Costs – Eliminate the need to bring up waste rock.
🔹Sustainable Backfill – Use the sorted waste rock as backfill material, reducing surface stockpile pressure and improving underground stability.
Pithead or Excavation Site Sorting
Many wonder where to best apply our sensor-based ore sorting equipment in the mining process. One great application is right at the start—at the Pithead or excavation site! 🚜 This is especially beneficial for mines with long distances to their Mineral Processing Plant. HPY’s XRT and VIS-HD colour sorting technologies can maximize the value of each transport, minimize tailings ponds, and help companies create extra profit by processing waste rocks and setting aside construction aggregate from the get-go.
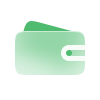
Average economic savings of 3.13 million USD per unit
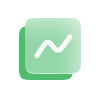
Improved sorting quality and reduced sorting costs
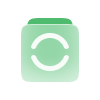
Mineral recovery rate of up to 98%
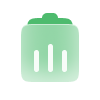
Rejection rate of up to 90%
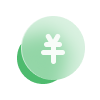
Low operation and maintenance cost of less than 0.2 USD per ton
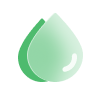
Reduced in water consumption
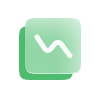
Significant decrease in energy consumption for grinding and flotation processes
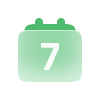
Reduced pressure and extended service life of tailings ponds
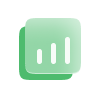
Improved mining extraction rate, comprehensive resource utilization rate, and mineral processing recovery rate
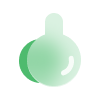
Reduced utilization of harmful chemicals used in traditional sorting processes