Economic Benefits
Fankou Construction Material Plant
977,000 USD per year in construction aggregate sales.
2.9 million USD per year lead-zinc waste rock recovery.
Fankou Mineral Processing Plant
2.2 million USD per year in economic benefits.
Project
With new underground mining processes, such as vertical crater retreat and large blasting, more waste rock is being introduced into the mineral processing plant, resulting in higher production costs and energy consumption.
Adding sensor-based ore sorting machines helped with the plant's mineral processing plant upgrade, reducing grinding costs, enriching the lead-zinc ore grade, reducing the amount of tailings entering the tailings pond, recovering ore from waste rock piles, turning waste rock into construction aggregates, and allowing the company to utilize their new underground mining processes by removing the excess waste rock early in the mineral processing process.
Case Study
Fankou Construction Materials Plant
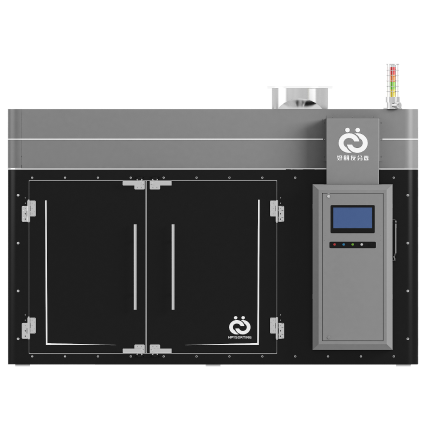
Raw Ore Grade: Pb 1.11% Zn 1.25%
Waste Rock Grade: Pb 0.04% Zn 0.10%
Concentrate Grade: Pb 10.74% Zn 11.6%
Recovery Rate: Pb 96.76% Zn 92.8%
Particle Size: +10-50mm
Rejection Rate: >90%
Enrichment Ratio: Pb 9.68 Zn 9.28
Fankou Mineral Processing Plant
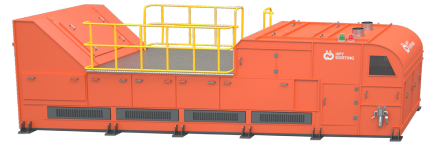
Processing Capacity: 2600t/d
Particle Size: +12-90mm
Raw Ore Grade: Pb+Zn 12%
Waste Rock Grade: Pb+Zn 0.3%
Grinding Grade: (Pb+Zn) increased by 1.08%
Rejection Rate: 16-17%
Interviewees
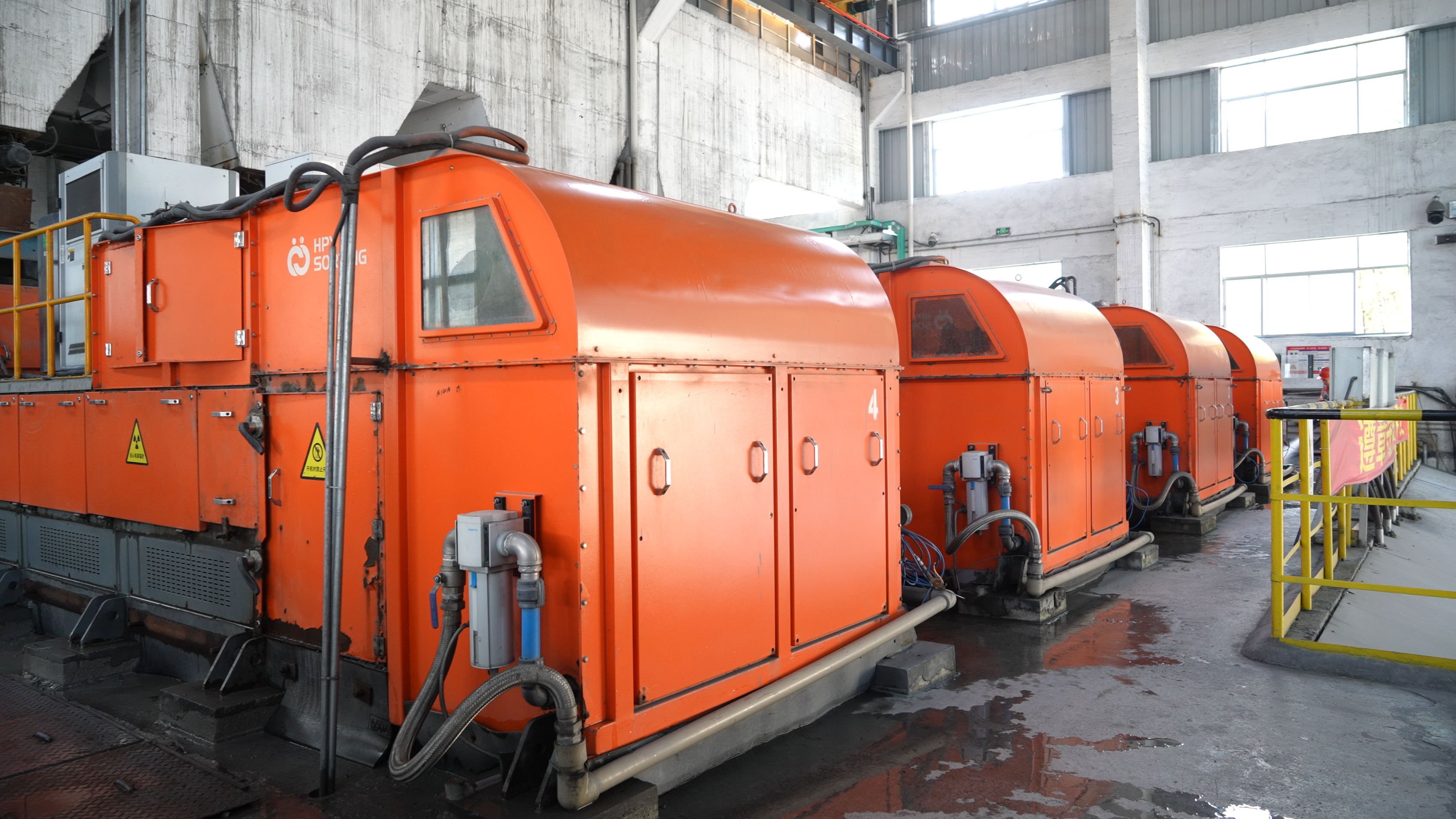
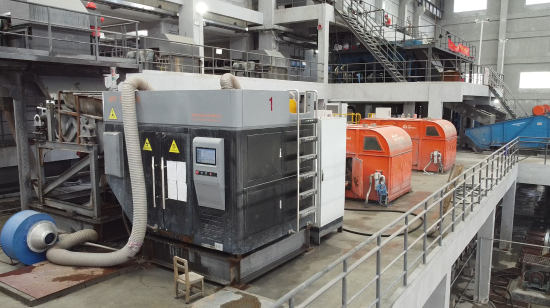
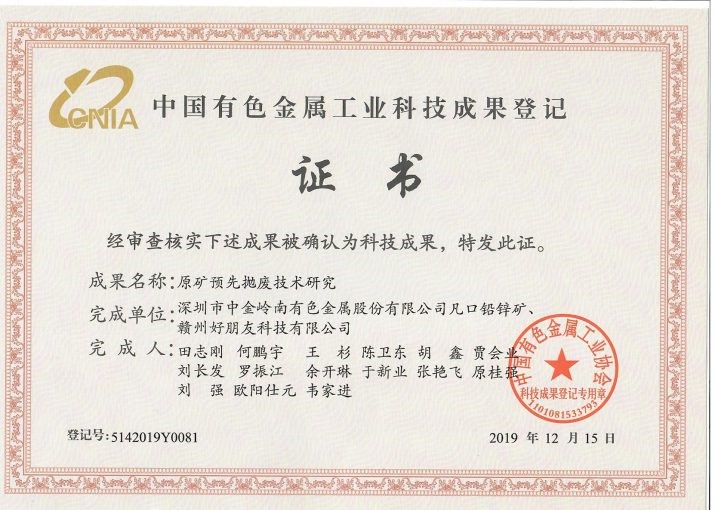
Interview With Zhongjin Lingnan
A: We first learned about HPY Technology at an industry exchange meeting in March 2018. At the time, there was no applications of sensor-based ore sorting for lead-zinc ore in China. The process flow consisted of high cost grinding and selection processes. Upon first learning of HPY’s XRT technology, we wanted to explore utilizing sensor-based ore sorting for lead-zinc ore and began collaborating with HPY.
At our mining site, we had over 2 million m2 of waste rock and our tailings pond was set to expire in 2025. Faced with significant environmental pressure, there was a need to reuse the waste rock stockpiles and lower the inflow of tailings into the tailings pond. Therefore, we planned to use ore sorting in our mineral processing plant to pre-concentrate the lead-zinc ore and remove waste rock early in the process, lowering the amount of tailings. We also looked to build a construction materials plant to reuse existing waste rock stockpiles, waste rock from excavation, and waste rock from the mineral processing plant to recover economically viable lead-zinc ore and produce construction aggregates.
We started the construction materials plant project with a processing capacity of 500 tons per day. HPY completed the testing in September 2018 and conducted onsite optimization in early 2019. The results met the government requirements for construction aggregates and lead to our process flow becoming a circular economy.
Previously to enrich the ore grade and minimize waste rock, we had to use small-scale blasting, but with the introduction of sensor-based ore sorting, we moved to large-scale blasting, which lowered our excavation costs. Additionally, adding sensor-based ore sorting to our mineral processing plant helped to enrich the ore grade entering the grinding circuit, reduce grinding costs, lower tailings pond inflow, and provide the option to remove waste rock to be sent to our construction materials plant for efficient resource utilization.
A: At our construction materials plant, which processes 500 tons per day, ore sorting can recover over 1,500 tons of lead-zinc resources per year from waste rock, generating a comprehensive overall revenue of 10.2 million USD.
In 2020, as a part of the plan for a new mineral processing plant, we added the XRT ore sorting machines into our process flow. At the time, due to the success in the construction materials plant, we purchased 4 Classic Series for pre-concentration. In September of 2020, we added an additional 3 ore sorters to our construction materials plant.
In January 2021, we officially installed the 4 Classic Series in our mineral processing plant and they were put into operation. These machines have brought significant improvements to our overall process flow and have created economic and environmental benefits for the company.
A: We believe that this technology provides a vast improvement and advancement to the overall process flow. It provides a great advantage for mines with low-grade ore, allowing for pre-concentration and the enrichment of the ore grade entering the grinding circuit. This technology also allows for improved resource utilization, allowing us to switch to large-scale blasting, because the low-grade ore will be enriched and the waste rock will be removed during the crushing stage. While there are around 90,000 mining companies in China, sensor-based ore sorting is still in its early stages, with less than 1% of mining companies using this technology. This leaves significant growth for the market as a whole, and for HPY. Which has proven its technological advancements, but has affordable pricing. We believe both technologically and in terms of pricing, their ore sorting machines have a distinct advantage in the international market. Many companies from China and other countries have visited our project to learn more about the use of sensor-based ore sorting. With the increased difficulty in mining and growing pressure on environmental issues, mining companies will focus on digitization, automation, and AI.
A: We are proud to be the first lead-zinc mine in China to use sensor-based ore sorting, and we have seen great results with the technology in our own operations. We believe that these machines can bring significant economic benefits to other companies, particularly projects with low-grade deposits. China has vast reserves of lead-zinc ore, ranking second globally, but the grades of these deposits are generally low, with an average grade of 1.5% for lead and 2.5% for zinc. More than 90% of reserves have a lead grade below 5.0% and more than 85% have a zinc grade below 8.0%. We want to share this innovative technology with our peers in the mining industry and contribute to the growth and progress of the mining sector.
A:Yes, China places a high emphasis on mines using more sustainable practices, providing both policy and financial support in this regards. Sustainability in mining covers a wide range of aspects, including mining and safety practices, production efficiency, management, environmental protection, resource utilization, and the overall aim of building an “environmentally-friendly” process flow. As companies struggle with either a buildup of waste rock stockpiles or issues in regards to their tailings pond, we have seen through our own project the benefit that HPY Technology and its machines can bring to these types of projects to address these environmental concerns.
A: We are excited to see that HPY Technology continue to introduce new products. We are impressed by their innovative capabilities, especially with the recent release of several new products. We have read about the product updates and have noticed significant progress compared to the machines we have previously purchased. Our current machines sort a particle size of +10mm-60mm, while the new products can sort particle sizes as small as 5mm, which offers a distinct advantage over other competitors. In comparison to the overall value created by the machines, we do not consider the cost of upgrading to be a concern. The total investment in constructing our new mineral processing plant is around 30 million USD, and it has been designed with the use of XRT ore sorting machines in mind. We have also modified our old production line with HPY Technology's machines, as we believe the modification cost is worth it considering the benefits brought by ore sorting.
"Our eco-friendly mine serves as a benchmark for future mine construction, safety, production, management, and environmental protection."