Tin, a versatile and valuable metal, has long been essential in various industries. Its unique properties, such as low toxicity, resistance to corrosion, and excellent soldering ability, make it indispensable in the modern world. However, the mineral processing of tin, a necessary step in obtaining this invaluable resource, has raised concerns about contamination and its potential environmental impact. This article will explore the importance of tin in industry, the possible contamination caused by its mineral processing, and how the innovative ore sorting technology, as demonstrated by Yunnan Tin Group's success, can help mitigate these risks.
The Significance of Tin in Industry
Tin's low melting point and exceptional flexibility make it an ideal choice for soldering, where it forms an essential component in the alloy. As electronic devices become increasingly complex and miniaturized, tin-based solders have become indispensable for ensuring reliable connections in circuitry. The automotive, aerospace, and consumer electronics industries all rely heavily on the tin in their manufacturing processes.
In addition to its role in soldering, tin is also used as a corrosion-resistant coating for steel. This application, known as tin-plating or electroplating, significantly extends the lifespan of steel products, such as cans, containers, and even automotive components. Tin also produces glass, catalyzes the float glass process, and creates high-quality, distortion-free glass.
Contamination Concerns in Tin Processing
The extraction and processing of tin are not without environmental risks. For example, Cassiterite, the primary ore of tin, often contains trace amounts of harmful elements, such as arsenic, lead, and other heavy metals. During the mineral processing of tin, these impurities can be released into the environment, leading to soil, water, and air contamination.
To reduce contamination risks, ore sorting technology has emerged as a promising solution. This technology employs sensors and advanced algorithms to identify and separate ore from waste material based on its physical and chemical properties. Ore sorting can reduce the volume of harmful elements released into the environment by pre-concentrating the ore before it enters the mineral processing stage.
Yunnan Tin Group and HPY Technology's Ore Sorting Solution
Yunnan Tin Group, one of the world's leading tin producers, has adopted HPY Technology's ore sorting machine to pre-reject waste rock, enabling them to mine resources in areas previously considered low-grade and burdened with excess waste rock. This innovative approach has allowed the company to utilize available resources better and resulted in substantial economic benefits and reduced environmental impact.
Yunnan Tin Group has achieved impressive results by incorporating HPY Technology's ore sorting machines. As a result, the company now pre-rejects 100,000 tons of waste rock per year, reducing mineral processing costs by 1.4 million USD, tailings pond expansion costs by 370,000 USD, and generating an additional 2 million USD in economic benefits. The raw ore grade at Yunnan Tin Group was Sn 0.456% and Cu 0.260%, while the waste rock grade was Sn 0.016% and Cu 0.077%. After implementing ore sorting technology, the concentrate grade increased to Sn 0.679% and Cu 0.368%, with a rejection rate of 36.8%. This demonstrates the effectiveness of ore sorting technology in improving resource recovery rates and reducing waste.
Tin's low melting point and exceptional flexibility make it an ideal choice for soldering, where it forms an essential component in the alloy. As electronic devices become increasingly complex and miniaturized, tin-based solders have become indispensable for ensuring reliable connections in circuitry. The automotive, aerospace, and consumer electronics industries all rely heavily on the tin in their manufacturing processes.
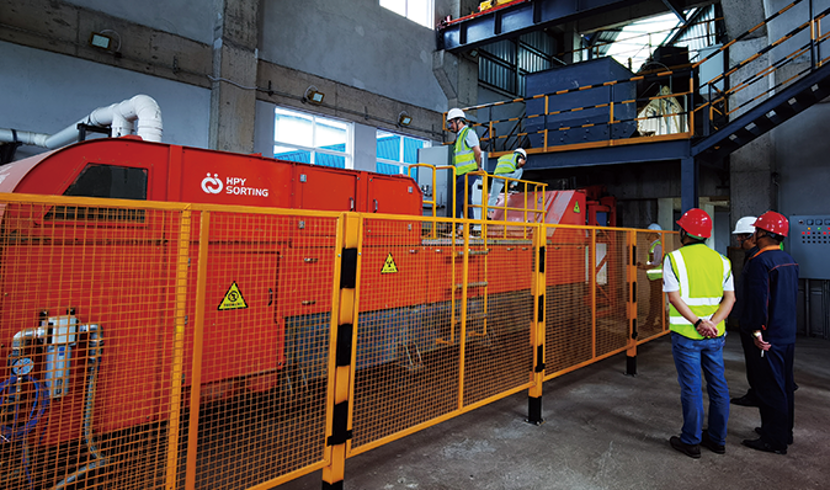
The success of Yunnan Tin Group in adopting HPY Technology's ore sorting machine showcases the immense potential of ore sorting technology in revolutionizing tin production. By pre-sorting and rejecting low-grade materials early in the process, mining companies can reduce costs, increase revenues, and mitigate the environmental impact of their operations.
Moreover, adopting ore sorting technology could unlock new mining areas previously considered unviable due to low-grade ore and excessive waste rock. This would contribute to a more sustainable and efficient tin production industry, promoting the responsible use of resources.
As the mining industry strives for sustainable and responsible practices, adopting innovative solutions like ore sorting technology will undoubtedly become more widespread. By embracing these advancements, the tin industry can continue to thrive while minimizing its environmental impact, paving the way for a more efficient and environmentally friendly future in tin production.