Ore sorting has been shown to provide both economic and environmental benefits, but many mines still need to utilize this technology fully. HPY Technology’s ore sorting machines are providing a breakthrough solution for Fankou, one of Asia’s largest lead and zinc mines, resulting in an annual revenue increase of around 9.22 million USD.
Located in Renhua County, Shaoguan City, Guangdong Province, Fankou is owned by Shenzhen Zhongjin Lingnan Nonfemet Co., Ltd. The mine has been producing lead and zinc for over 60 years. However, with new underground mining processes, such as vertical crater retreat and large blasting, more waste rock is being introduced into the crushing, grinding, and flotation processes, resulting in higher production costs and energy consumption.
Furthermore, under the “zero waste” target set by the Environmental Protection Law of China, Fankou’s tailings pond needs to be closed by 2025. As of 2018, the mine’s annual processing capacity was 1.5 million tons, with 600,000 tons ending up in the tailings pond. In addition, Fankou’s waste rock piles had reached approximately 2 million tons. With the continuous addition of around 200,000 tons of waste rock each year, these piles grew larger. With the pressure to meet the “zero waste” target, Fankou was under pressure to make a change.
In 2017, Fankou conducted exploratory tests of sensor-based ore sorting machines with Ganzhou HPY Technology Co., Ltd. The result of the initial tests showed promise and addressed the problems the mine was beginning to face. As a result, Fankou decided to add HPY’s ore sorting machines to the industrial design plan of their mineral processing plant in 2018, and HPY’s machines were officially added in 2019.
The Fankou lead-zinc mine currently produces about 1.4 million tons per year in ore, and it is expected that more than 105,000 tons of waste rock will be pre-rejected from the raw ore throughout the year. Ore sorting technology can discard a large amount of waste rock from the raw ore before it is fed into the flotation system, reducing the amount of waste rock entering the mill and saving on electricity costs.
Fankou’s mineral processing plant uses 4 Classic Series P60-X1400 ore sorting machines. The machine processes the particle size range of +12-90mm, which accounts for about 50% of the raw ore. This accounts for 2,600 tons of ore, rejecting 400-500 tons of waste rock daily. After pre-concentration, the lead and zinc in the waste rock are below 0.3%, and the sulfur and iron content is below 3.8%. Therefore, the ore sorting process enriches the ore grade by 1.08% for lead and zinc and 2% for sulfur and iron.
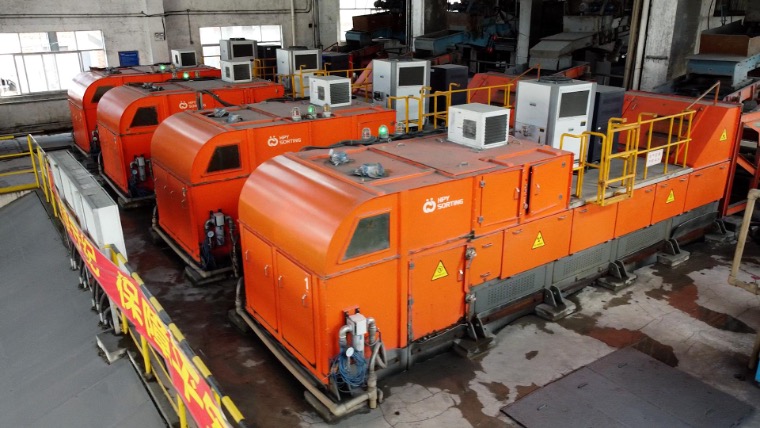
After sorting the waste rocks from the raw ore, the waste rocks can be sold as construction aggregates to bring further economic benefits to the Fankou mine. Due to the reduction of waste rock in the raw ore, the amount of tailings has decreased, and the service life of the tailings pond has been significantly elongated, which has achieved remarkable performance in energy saving and consumption reduction, which also enhances the mine’s societal value.
“We are proud to be one of the world’s first lead and zinc mines to utilize ore sorting fully. We see significant economic benefits for using HPY Technology’s ore sorting machine, especially for low-grade mines. China has huge lead and zinc ore reserves, the second largest in the world. But the grade of the deposits is generally low, with many poor and few rich ores. The average grade is about 1.5% for lead and 2.5% for zinc. Reserves with a grade below 5.0% account for more than 90% of lead ore, and reserves below 8.0% account for more than 85% of zinc ore. We hope to continue contributing to the mining industry’s progress and are willing to recommend HPY Technology’s ore sorting machine to our peers.” -Mr. Wang, Project Manager of Fankou Mineral Processing Plant
The Classic Series used in Fankou’s mineral processing plant is a benchmark in the ore sorting industry. This machine utilizes dual-energy X-ray technology, combined with high-speed air jets to sort ore from waste rock. The X-ray technology penetrates the ore and creates a grayscale image that distinguishes between target and vein minerals. This image is then processed by an AI algorithm, which uses the information to accurately sort the ore and waste rock. The Classic Series has undergone numerous iterations, ensuring stable and efficient operation. It is currently the most widely used ore sorting machine in China’s mining industry.
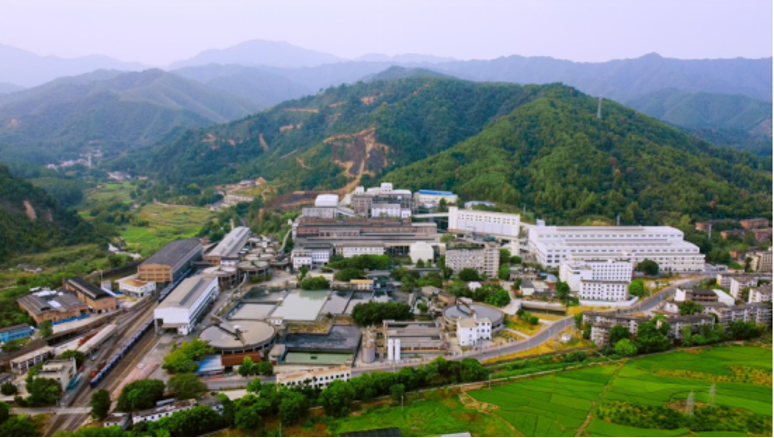
HPY Technology | Fankou Lead-Zinc Mine, Mineral Processing Plant | |
---|---|
Machine Used | 4 Classic Series P60-X1400 |
Processing Capacity | 2600 t/d |
Particle Size | +12-90mm |
Concentrated Ore Grade | (Pb+Zn) 12% |
Waste Rock Grade | (Pb+Zn)<0.3% |
Grinding Grade | (Pb+Zn) increased by 1.08% |
Rejection Rate | 16-17% |
Fankou’s mineral processing plant can save more than 2.9 million USD per year by using HPY’s ore sorting machines, resulting in an annual profit margin of more than 7.8 million USD, considering the comprehensive benefits of increased plant capacity, tailings reduction, and construction aggregate sales.
In addition to the 4 Classic Series P60-X1400 in the mineral processing plant, the construction materials plant has 3 HPY ore sorting machines to process the waste rock from the mineral processing plant and its existing waste rock piles. The waste rock is taken to the construction material plant for another round of sorting, with the remaining waste rock being used for construction aggregates. The 3 machines at the construction materials plant also process the 2 million cubic meters of waste rock initially stockpiled in the tailings pond.
“In the past, we could only transport solid waste back to the shaft for filling. After using HPY’s ore sorting machines, we can now sort out all the ore from solid waste and recover the value of the resources. The remaining waste rock can be sold as construction aggregates, which is a win-win solution. Currently, we are also sorting waste rock that was stored before using HPY’s ore sorting machines. The ore grade is about 3%. Sensored-based sorting technology enriches the ore grade to 12% to 14%. Sorting results show that the rejection rate exceeds 95%. In the global mining industry, Fankou is one the first to successfully apply intelligent ore sorting technology in lead and zinc mines, achieving maximum resource value recovery and is great for the environment.” -Mr. Luo, Project Manager of Solid Waste Treatment
According to Mr. Luo, waste rock that was initially made into construction aggregates now yields more than 1,500 tons of lead and zinc metal every year, which has been able to be recovered through the Construction Materials Plant. In addition, the ore sorting process reduces the waste rock’s sulfur content. This substantially improves the grade of the construction aggregates, increasing their sales price. As a result, the waste rock made into construction aggregates generates about 977,000 USD per year in economic benefits. In addition, the recovered ore generates over 2.8 million USD per year in benefits.
Fankou has utilized sensor-based ore sorting to its full extent. Using it during the comminution process to pre-reject waste rock to increase its lead-zinc ore grade. The company also sees benefits from pre-rejected waste rock in reduced costs in their grinding process. With pressure to control the amount of tailings, the pre-rejected waste rock lowers the amount of tailings entering the tailings pond to help the company close the tailings pond in 2025. In addition, sensor-based ore sorting has allowed the company to gain additional revenue through the recovery of lead-zinc from their waste rock piles, while also utilizing these piles for construction aggregates. Overall, the introduction of ore sorting has allowed the company to expand its resource recovery. By pre-rejecting and enriching low ore grades, Fankou can now mine areas previously deemed unmineable due to having low grade ore, allowing them to increase the processing capacity each year.
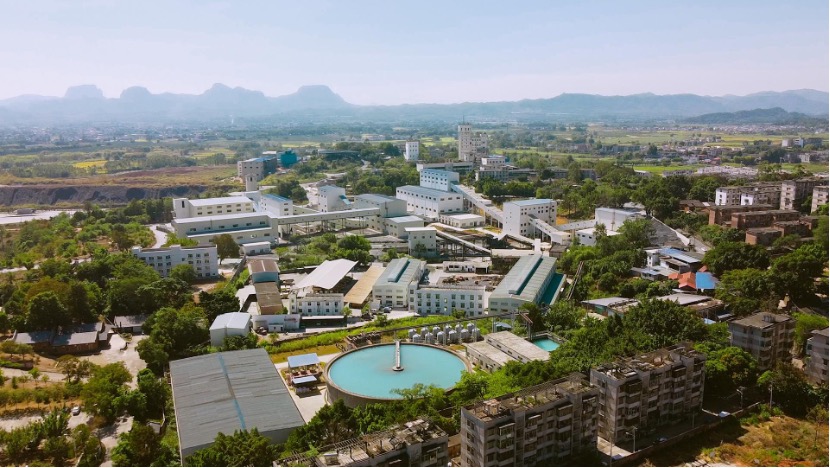
HPY Technology | Fankou Lead-Zinc Mine, Construction Material Plant | |
---|---|
Machine Used | 1 Insight Series | 2 Classic Series |
Concentrated Ore Grade | 12% - 14% |
Waste Rock Grade | Pb 0.04% Zn 0.10% |
Concentrate Recovery Rate | Pb 96.76% Zn 92.8% |
Rejection Rate | 95% |
Enrichment Ratio | Pb 9.68 Zn 9.28 |
Particle Size | +10-50mm |
The Insight Series used in Fankou’s Construction Materials Plant adopts a combined detection method composed of a VIS HD dual-sided imaging system and X-ray technology, which can be customized according to the physical characteristics of different ores. The machine can collect the ore’s internal and external information simultaneously and with an AI algorithm, which can significantly improve the accuracy of ore sorting and better for sorting complex ores.
Compared to traditional ore sorting machines, which use a belt, the upgraded Insight Series utilizes a vibrating feeder and short belt that leads to ore free fall. With the optimized mechanical design, the ore falls more evenly, avoiding ore overlap that affects recognition accuracy. In addition, the machine has various feeding widths (1600mm, 3200mm), which leads to processing capacities of 40-150 tons per hour (+10mm-80mm) to meet the needs of different mines needs during the beneficiation process.
As one of Asia’s largest lead and zinc mines, Fankou has taken steps to maximize the economic value of its process. Through the utilization of sensor-based ore sorting, the company has seen significant increases in revenue and savings. Having worked with HPY for over 5 years, Fankou looks to continue this partnership to further the research on the benefits of ore sorting machines. As HPY Technology continues innovating and revolutionizing mineral processing, the benefits will only continue to grow.
HPY Technology Co., Ltd. is a leader in the development and manufacture of ore sorting machinery, achieving excellent results in the ore sorting of tungsten, tin, antimony, lead, zinc, copper, molybdenum, gold, phosphate, and over 30 other ore types, revolutionizing the traditional mineral processing process, and significantly promoting the technological progress of the global mining industry. With over 400 machines in use in over 100 mines, the company looks to continue revolutionizing mineral processing.